I was lucky enough to find myself once again in striking distance of Bletchley Park yesterday and enjoyed another interesting visit. Just like last time, the Battle of Britain Memorial Flight treated us to a fly-past - this time by a Spitfire...
![]()
Having last time focussed much attention on Colossus, I was determined to spend a little more time looking at the Bombe (which itself has been the subject of a re-build project) ...
![]()
I was fortunate to be able to chat with one of the guides, who explained in considerable detail the operation of this impressive machine. I don't know her name or her background, but she certainly understood operation of the Bombe in depth and I am grateful for her expertise.
Talking about expertise, I was pleased to chat once again with David Wright, g3zpa, who gave me some more information about the original (long-wire) antenna systems supplied for use with the Paraset.
In addition to the aircraft flypast, there was an impressive gathering of classic cars with the inevitable superabundance of MGs (I'm allowed to say that as an MGB owner)...
![]()
However, other marques were well represented too. The car of the show (for me at least) was a drop-dead-gorgeous Alfa Giulia Veloce - but I was pleased to see some nice 3-wheeler Morgans...
![]()
These 3-wheelers are of interest partly because the XYL's grandfather used to own one and partly due to their pivotal role in the plot of Dorothy Leigh Sayers' "Have His Carcase". Morgans more generally have a place in my heart as the XYL and I went on honeymoon in a 4-4. Happy days!
Cars and aeroplanes aside, there was lots more to interest me at BP - not least in my first visit to The National Museum of Computing which, appropriately, is in the same building as Colossus. After seeing the PDP8's of my youth I was pleased to see a healthy display of analog computers (which - for those of you who don't know - solve differential equations by electrical ANALOGY) amongst which was something I'd never seen before: a hybrid analog AND digital computer...
![]()
In truth, it was an analog computer with a few digital elements (flip-flops etc) along the bottom "row" in the photo above.
I was also delighted to find an example of the main board from a Tangerine "microTan 65"...
![]()
One of my first computers was built around this 6502-based system marketed as a kit by Tangerine. There was a basic interpreter, a disk operating system and all sorts of goodies. Nice to see it again!
However, the high spot of my visit to the National Museum of Computing was certainly the Domesday systems, based on BBC / Acorn hardware and in the news recently because of the "Domesday reloaded" initiative. Here's one of the two working systems at BP...
![]()
We were staying with the in-laws, near Pulloxhill, Beds., so we used the amazingly modern multi-media interface to search for Pulloxhill and pulled up a picture of the characteristic water tower...
![]()
Here's a link to the photo on the web-based Domesday Reloaded resource.
Partly (I am told) in consequence of the recent financial debacle at the RSGB, the new radio centre isn't yet open to visitors...
![]()
... but we did call into the MKARS club house (in an old generator building on the BP "campus") where I had a nice chat with Graham, a G7 licensee (I missed the rest of his call), before driving back to Pulloxhill.
On the drive back we stopped to take an up-to-date shot of the water tower...
![]()
Sitting outside drinking a cup of tea half an hour later, the day was crowned by an unexpected flypast of a Consolidated Catalina, the conspicuous lines of which were unmistakable even at altitude...
![]()
I assume she was G-PBYA, which is "berthed" at Duxford - she certainly was heading in the right direction!
Perfect end to a(nother) grand day out!
...-.- de m0xpd
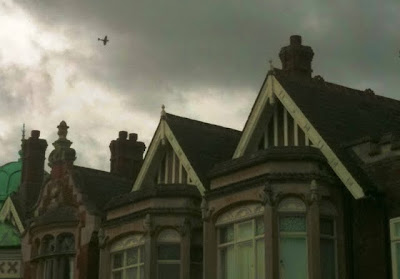
Having last time focussed much attention on Colossus, I was determined to spend a little more time looking at the Bombe (which itself has been the subject of a re-build project) ...
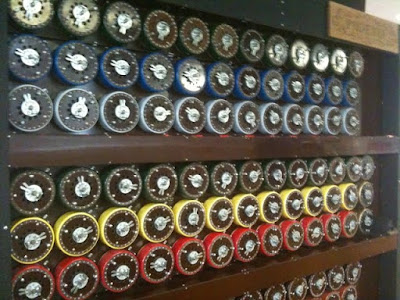
I was fortunate to be able to chat with one of the guides, who explained in considerable detail the operation of this impressive machine. I don't know her name or her background, but she certainly understood operation of the Bombe in depth and I am grateful for her expertise.
Talking about expertise, I was pleased to chat once again with David Wright, g3zpa, who gave me some more information about the original (long-wire) antenna systems supplied for use with the Paraset.
In addition to the aircraft flypast, there was an impressive gathering of classic cars with the inevitable superabundance of MGs (I'm allowed to say that as an MGB owner)...
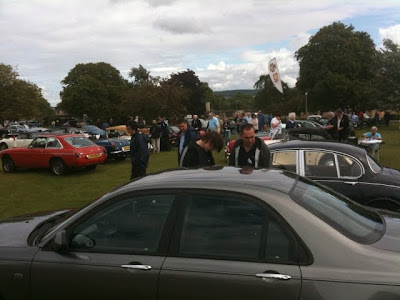
However, other marques were well represented too. The car of the show (for me at least) was a drop-dead-gorgeous Alfa Giulia Veloce - but I was pleased to see some nice 3-wheeler Morgans...
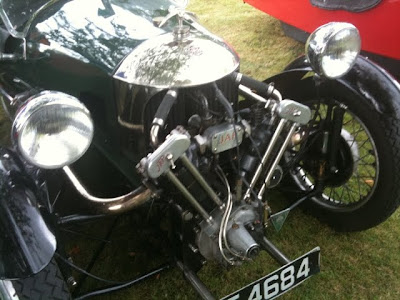
These 3-wheelers are of interest partly because the XYL's grandfather used to own one and partly due to their pivotal role in the plot of Dorothy Leigh Sayers' "Have His Carcase". Morgans more generally have a place in my heart as the XYL and I went on honeymoon in a 4-4. Happy days!
Cars and aeroplanes aside, there was lots more to interest me at BP - not least in my first visit to The National Museum of Computing which, appropriately, is in the same building as Colossus. After seeing the PDP8's of my youth I was pleased to see a healthy display of analog computers (which - for those of you who don't know - solve differential equations by electrical ANALOGY) amongst which was something I'd never seen before: a hybrid analog AND digital computer...
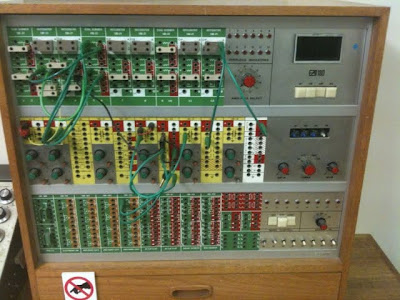
In truth, it was an analog computer with a few digital elements (flip-flops etc) along the bottom "row" in the photo above.
I was also delighted to find an example of the main board from a Tangerine "microTan 65"...
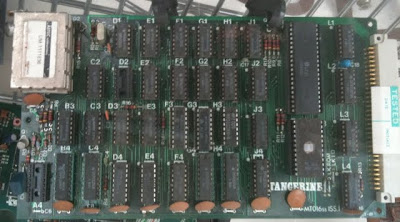
One of my first computers was built around this 6502-based system marketed as a kit by Tangerine. There was a basic interpreter, a disk operating system and all sorts of goodies. Nice to see it again!
However, the high spot of my visit to the National Museum of Computing was certainly the Domesday systems, based on BBC / Acorn hardware and in the news recently because of the "Domesday reloaded" initiative. Here's one of the two working systems at BP...
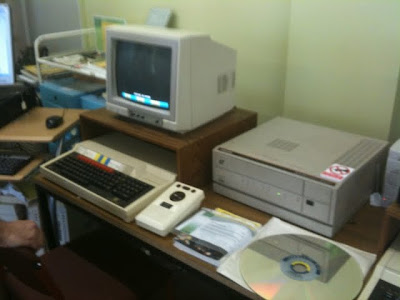
We were staying with the in-laws, near Pulloxhill, Beds., so we used the amazingly modern multi-media interface to search for Pulloxhill and pulled up a picture of the characteristic water tower...
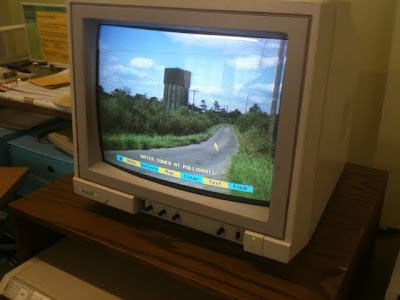
Here's a link to the photo on the web-based Domesday Reloaded resource.
Partly (I am told) in consequence of the recent financial debacle at the RSGB, the new radio centre isn't yet open to visitors...
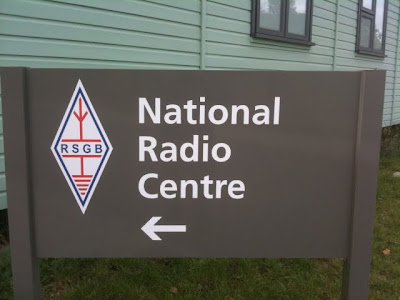
... but we did call into the MKARS club house (in an old generator building on the BP "campus") where I had a nice chat with Graham, a G7 licensee (I missed the rest of his call), before driving back to Pulloxhill.
On the drive back we stopped to take an up-to-date shot of the water tower...
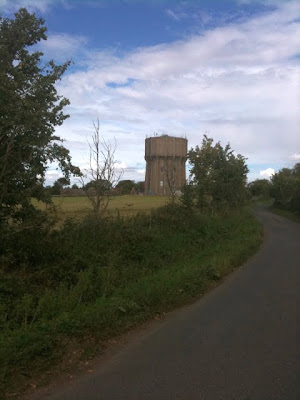
Sitting outside drinking a cup of tea half an hour later, the day was crowned by an unexpected flypast of a Consolidated Catalina, the conspicuous lines of which were unmistakable even at altitude...
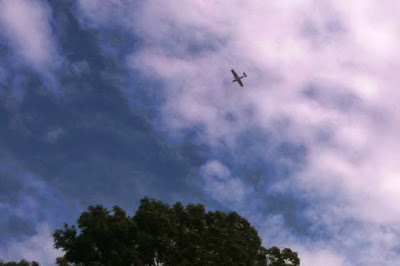
I assume she was G-PBYA, which is "berthed" at Duxford - she certainly was heading in the right direction!
Perfect end to a(nother) grand day out!
...-.- de m0xpd